“This thing here, which looks like a wooden club, is actually several pieces of particular wood cunningly put together in a certain way, so that the whole thing is sprung, like a dance floor. It’s for hitting cricket balls with. If you get it right, the ball will travel two hundred yards in four seconds, and all you’ve done is give it a knock, like knocking the top off a bottle of stout, and it makes a noise like a trout taking a fly. What we’re trying to do is to write cricket bats, so that when we throw up an idea and give it a little knock, it might travel.”
For what are essentially ‘chunks of wood,’ English playwright Tom Stoppard, although referring to writing, once offered this most poetic description of a cricket bat. We, as enthusiasts, might or might not indulge in this romance, but do we invest in the expensive ones occasionally. Professionals spend up to five digits. A bat that looks like Virat Kohli’s could set you back by anywhere between Rs 25,000 to Rs 35,000, while the one that he uses would be far costlier.
Batmakers think they tender enough value for this money. A truly exquisite bat is made from the purest timber. The wood is then machined, to carve the perfectly hardened blade (the front) and a back that is curvy enough to generate power. The handle, a shock-absorbing piece of rubber-infused cane, is spliced into the blade and filed flush with the wood. The toe is coated with special materials to make it resilient, and the final product is then sealed with durable silicon wax. This is just the manufacturing; the process of knocking in, or making it game-ready, then follows.
However, unlike say the tennis racket or the football, which have undergone rapid technological upgradation over the last few decades, the cricket bat has, barring cosmetic changes, remained mostly unchanged in terms of design and materials since at least the 1970s, when the English company Gray-Nicolls launched its revolutionary GN100 Scoop bat, which took its name from the fact that it was made by taking out a large ‘scoop’ of willow from the back of the blade, which in turn had the effect of not just making the bat lighter, but also widening its ‘sweet spot’ beyond the conventional ‘dead centre’. The Scoop ensured that a batsman’s shot would still travel to the boundary at the same pace even it wasn’t hit off ‘dead centre’.
The bat became a rage in the UK, Australia and New Zealand in the 1970s and ‘80s, after the success it had with the likes of the Chappell brothers, David Hookes, Lawrence Rowe, Clive Lloyd, David Gower and more. India, though, with its import restrictions, remained mostly untouched by the Scoop’s popularity; it is only in recent times that the bat has become available in the country. Though India continues to be among the world’s biggest manufacturers of cricket bats, the makers have never been known for innovation in design or technology.
Two Mumbai-based friends, Kunal Joshi and Aayush Tapuriah, hope to change all that with their new company Elevar Sports, a start-up with the mission to design and make bats that ‘reflects the values of the New Age cricketer’. Elevar is a Spanish word, which translates to ‘raise’ in English. “We started Elevar because we absolutely love cricket, but despite years of trying, we could not fall in love with a cricket bat. At different times, bats have let us down in terms of performance, reliability and style. We felt this gap only increase with time. Cricket continues to evolve into a more dynamic sport, while the incumbent brands of bats are not really keeping up,” says Tapuriah.
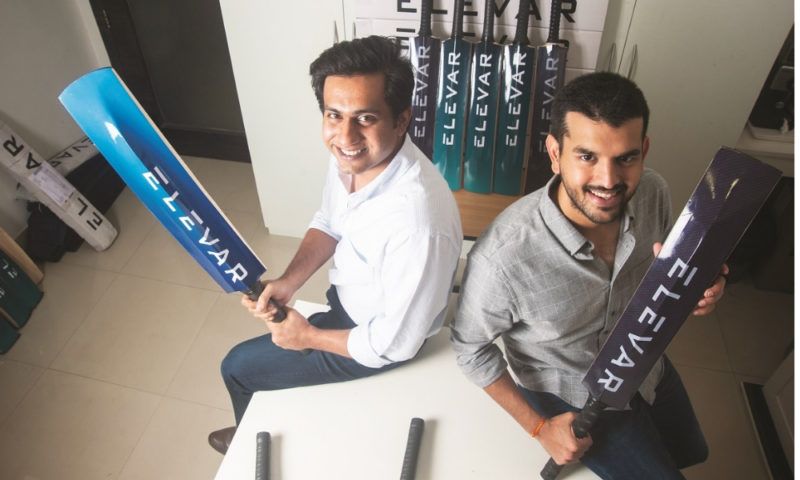
The duo met in 2007, while students at Cornell University, but went their separate ways. Ten years later, their shared passion for cricket reunited them. Joshi decided to quit a high-paying job at Temasek Holdings, and Tapuriah chose to return home after finishing his MBA at Wharton, to finally pursue their dream of building a cricket brand. They believe that while the game might have evolved into its hard-hitting, swashbuckling form today, the technology involved in making bats remains archaic. They point to YouTube videos of bat manufacturing processes in England, and call it ‘as automated as it gets’’ “It’s a very manual and labour intensive process, and the abundance of cheap person power makes India the manufacturing hub,” Joshi says.
“GM (Gunn & Moore) is being made in Jalandhar, while Kookaburra bats are made by SG (Sanspareils Greenlands), and stickers are put on them,” says Tapuriah. “India dominates the bat-making industry because of the large market, as well as better manufacturing economics as compared to England and Australia. The likes of GM, Grey Nicolls, Slazenger, Kookaburra etc don’t have any R&D. They don’t have many product designers or engineers on their teams. It’s pretty much wood being carved to predefined specs at scale. There has been no real innovation in bat-making. It’s been the same for decades.”
The low-hanging fruit of technologically designing bats, according to him, has therefore always existed. However, since bat-making is a traditional family business, no one is in it for the innovation. Elevar’s team, on the other hand, comprises industrial designers and engineers who apply science and design-thinking to understand how a bat should be made from the ground-up. “We started with clay models of how people hold a bat and then drew inspiration from objects with similar mechanics, ranging from baseball bats to samurai swords,” Tapuriah says. They made numerous prototypes and conducted experiments to measure the comfort and performance achieved using prototypes. The first bats were launched this May after nearly a year of prototyping.
“As a startup, we constantly have to be creative. Our immediate goal is to stand out as a cricket brand that’s very different from what’s out there, one that pays attention to product design and drives innovation through science and engineering,” Joshi says. This argument might hold water. Remember when tennis used to be played with wooden rackets? Then burst forth a certain Howard Head in 1975. He registered his revolutionary oversized frame with the US patent office, and when it – as the Prince Classic – hit the market a year later, the act of striking a tennis ball, as expressed by Sports Illustrated, would never be quite the same. The fairness of this comparison might be questionable given cricket bats have to be made of wood, but a closer parallel is the baseball bat. New two-piece bat designs have gained popularity in the recent past, while today, companies like Axe Bat are bringing in innovations like an axe-like handle for a better swing.
Cricket, on the other hand, has not seen a change as radical about its equipment. Former Indian cricketer Sanjay Manjrekar can be seen comparing the bat from his playing days (the early ‘90s) to a current one in a 2014 video for ESPNCricinfo. In the entirety of his four-odd minutes of elucidation, he can hardly point out anything significant, other than a thicker edge and the resulting bat strength.
The counter-argument to that would be centred around the International Cricket Council’s (ICC) rules governing the shape and size of bats. The folks over at Elevar, though, promise that much more can be done even within these rules. By employing a novel methodology, they have re-imagined three essential defining factors – the handle, the grip and the blade.
“An ideal bat handle should have a different shape profile at the top and the bottom, because both hands perform fundamentally different functions,” Joshi says. By seeking inspiration from Japanese samurai swords, Elevar’s dual-design handle claims to offer better ergonomics and bat control.
When it comes to the grip, the market survey spoke about losing control of the ball when ‘not middled’ well. Elevar asserts that this can be resolved by layering the bottom of the grip with an industrial grade polymer. This material has far superior vibration damping ability than rubber alone. Elevar’s engineers chose this technology after they tested hundreds of different materials and their impact on energy transfer. As for the blade, Elevar’s engineers make subtle adjustments to the shape of each bat, to ensure that the balance and lift of the bat stay similar. Team Elevar has found that players respond better to similarly balanced bats, as opposed to bats with similar dimensions. Unsurprisingly, the managing director of Gunn & Moore, Peter Wright, also made similar remarks about his company’s bat-making science in an interview with The Telegraph.
Though there are testimonials from a handful of ex-Ranji cricketers on their website, we got our own bat tester in the nets for a first-hand look at Elevar’s claims. Sarfaraz Khan, the explosive star of the 2014 and 2016 Under-19 World Cups, who now plays for Royal Challengers Bangalore in the IPL, obliged us on a bright Saturday afternoon in Mumbai, along with his father Naushad, a renowned coach in the city’s cricketing circuit. Both used the Elevar English at Mumbai’s famous Azad Maidan during a local club game.
“The two good things about the bat are its grip and the handle,” says Naushad. “We, as coaches, emphasise cocking of wrists while training budding cricketers. It’s the opening up of the top hand, in turn opening the face of the blade easily. With the help of a sharp edge rather than a rounded one on the top hand, cocking becomes almost like an automatic process.” Sarfaraz adds “The same design might also prove helpful while rolling the wrist on the bottom hand to play on the leg side, but it might be a little difficult against speeds of 140-150 kph, when you don’t have much margin of error. It will still need a few more weeks for me to figure that out.”
The quality of the willow might not be the strongest suit of Elevar’s bats, and that is the only negative that both Sarfaraz (who usually plays with grade 1 willow and above) and Naushad have to offer. “It’s exciting to see such a company being set up in India,” Naushad remarks. “That too from Mumbai. I’ve always been a proponent of introducing science, technology and analysis tools into cricket.”
Tapuriah says that the company’s immediate focus might not be on the willow quality, because the bread and butter products for them remain the two less-professional models in the Elevar Gully (for tennis ball cricket, priced at Rs 1,500) and Elevar Kashmir (for leather ball beginners, priced at Rs 3,000). Elevar English, which Sarfaraz tested, is currently priced at Rs 12,500 and is targeted at professionals. It is still a work in progress and will see the quality improve with feedback from the players.
“The pros, anyway, get their bats custom-made,” Tapuriah says. The big guns get what they want, but Elevar believes that the beginners and masses fall for the trap of branding. They will buy an MRF bat just because Sachin Tendulkar has endorsed it, but MRF doesn’t engineer bats. That is precisely what this new startup is aiming to counter. Instead of buying something based on a sticker, they want to build a brand that stands for innovation and science.
Willow Grading
Very best Grade 1+ willow
The English willow blade is unbleached with 8-12 straight grains and is blemish free. Price range around Rs 30,000
Grade 1 willow
As, above but with a slightly broader grain and sometimes a slight red edge. Price range around Rs 20,000
Grade 2 willow
Unbleached English willow with some minor blemishes, red wood on the edge and a slight irregular grain. Price range around Rs 15,000
Grade 3 willow
Some of these bats will be bleached English willow to cover up a more irregular grain and more blemishes. Price range Rs 10,000
Grade 4 willow
Bleached English willow, which is often covered up with a protective facing and sold as “non oil”. Price range around Rs 7,500
Kashmir willow
Harder and dryer by nature than English willow, so doesn’t last as long. Ideal starter bat. Price range around Rs 5,000
“One of the most simple innovations on our Gully bat is using polyurethane as a grip material, rather than the traditional rubber,” says Tapuriah. “The rubber grips on cricket bats are designed for use with gloves, but a majority of cricket is played barehanded. We use a similar material as in tennis, badminton, and squash rackets to make barehanded play more comfortable. It’s simple things like these that incumbent bat-makers have simply not thought through. The round shape of handles has come about because it’s easier to make at scale, not because it’s more ergonomic. Handles in the good old days, in fact, used to be oval,” he points out.
Elevar’s bats, which were launched this May, can, currently only be purchased on their website; they’re aiming to sell 1,500 units a month. The bat that we got for the Khans was from the batch that had just been shipped under the supervision of the design head of the company, who is almost always out at their three manufacturing hubs – Jammu & Kashmir, Meerut and Jalandhar – to ensure the requisites are met. Then there’s an operations manager, and a tech person (a robotics engineer), who also takes care of the website, in this ‘bare bones, basic’ team.
“In terms of product roadmap, we want to keep upgrading the cricket bat in one or two-year cycles,” Tapuriah tells us. “We feel that a bat should be no different from a shoe. Every year, shoe brands unveil different innovations in material, design, and functionality. We have a bunch of hypotheses that we want to research for innovations in bat design. Apart from this, we will look to launch other sporting products, but always with the focus on innovation and design, rather than just putting out more of what’s already out there.”
Elevar’s partners are cagey in terms of finances. “Elevar doesn’t need to raise funding immediately, for ‘bat-making is a profitable business,” is all they would say. They admit that doing so would become imminent once they manufacture newer products. One big difference from some of the precedents – in tennis and baseball – is that they’re not patenting their designs. They maintain that if someone like an SG puts out a bat with a handle design like theirs in the future, that would be a good parameter of success. What matters to them is the process of innovation and invention; maybe that’s the new precedent.
How are bats made?
- A trunk of willow is shaped into roughly cricket bat-sized chunks known as clefts. Before being carved into a more familiar-looking bat shape, their ends are dipped in wax, and they are air-dried for up to a year
- At this point, the clefts are graded into four levels, which is done by a master craftsman inspecting the bat. Criteria include the straightness of the grain, width of the grain, any blemishes etc. It is worth noting that, while a Grade 1 bat will probably look superior, there is no guarantee that it will actually play better than, say, a lower-ranked Grade 4 bat
- Then the bat goes through the pressing process, where it is slowly compressed into shape via a machine
- The blade is then spliced at the top and a handle attached, which is key in providing the almost spring-like capabilities of the bat
- Once the shoulders have been cut out, more specific alterations are made to the timber by hand, such as rounding off the toe and filing away unnecessary pieces.
- After the edges and face have been sanded down, the bat is polished by a bee’s wax compound, which helps to keep moisture out and let linseed oil in
- The handle is bound by string, and modern additions such as the rubber grip and maker’s stickers are applied